Steel vs Traditional Construction: A Complete Comparison - Making the Right Choice for Your Home
- Josef Doctorovitz
- Nov 13, 2024
- 5 min read
In recent years, residential steel building kits have emerged as a compelling alternative to traditional wood-frame construction. As homeowners seek more efficient, durable, and sustainable building options, the debate between steel and traditional construction methods has become increasingly relevant. This comprehensive comparison will help you understand the key differences between these two construction methods and make an informed decision for your next building project.
Understanding the Initial Investment
The upfront costs of construction often play a crucial role in decision-making. Residential steel building kits typically require a higher initial investment compared to traditional wood construction, with prices ranging from $20-30 per square foot for basic steel structures versus $15-20 per square foot for conventional wood framing. However, this simple comparison doesn't tell the whole story.
Steel building kits come pre-engineered and ready to assemble, which significantly reduces labor costs and construction time. While the materials themselves might cost more, the overall project cost can often be comparable or even lower than traditional construction when factoring in reduced labor expenses and faster completion times.
Additionally, steel prices tend to be more stable than lumber prices, which can fluctuate dramatically based on market conditions and seasonal factors. This stability makes it easier to budget and plan for your construction project without worrying about sudden price increases.
Construction Timeline Advantages
One of the most significant advantages of residential steel building kits is the speed of construction. Traditional wood-frame construction typically takes 6-12 months to complete, depending on the size and complexity of the project. In contrast, steel buildings can often be erected in just 1-3 months.
This accelerated timeline is possible because steel building components arrive pre-engineered and ready to assemble. Unlike traditional construction, which requires extensive on-site cutting, measuring, and fitting, steel buildings follow a precise assembly process. This not only speeds up construction but also reduces the likelihood of errors and delays.
Weather delays also have less impact on steel construction. While wood framing requires dry conditions for installation and can be damaged by moisture during construction, steel components can be installed in various weather conditions without compromising structural integrity.
Long-Term Maintenance Considerations
The maintenance requirements for steel and traditional construction differ significantly. Wood-frame homes require regular maintenance to prevent issues like rot, termite infestation, and water damage. This includes periodic treatments for pest control, repainting or residing, and replacing damaged wood components.
Residential steel building kits, on the other hand, require minimal maintenance. Modern steel buildings are treated with protective coatings that prevent rust and corrosion, often lasting decades without requiring significant upkeep. The primary maintenance tasks involve routine inspections of joints and connections, and occasional cleaning.
Durability and Structural Integrity
When it comes to durability, steel construction holds a clear advantage. Steel buildings are engineered to withstand extreme weather conditions, including high winds, heavy snow loads, and seismic activity. The strength-to-weight ratio of steel is superior to wood, allowing for larger clear spans and more open floor plans without compromising structural integrity.
Steel doesn't warp, crack, or split like wood can over time. It's also impervious to termites and other pests that can compromise wooden structures. Fire resistance is another crucial advantage – while wood-frame buildings can be quickly consumed by fire, steel maintains its structural integrity at high temperatures, providing valuable extra time for evacuation and firefighting efforts.
Energy Efficiency Benefits
Modern residential steel building kits are designed with energy efficiency in mind. The precise engineering of steel components allows for optimal insulation installation, reducing thermal bridges commonly found in wood-frame construction. When properly insulated, steel buildings can achieve excellent energy efficiency ratings.
Steel buildings can be designed to incorporate energy-efficient features such as cool roofs, solar panels, and advanced HVAC systems more easily than traditional construction. The thermal mass of steel can also help regulate indoor temperatures, potentially reducing heating and cooling costs over time.
Insurance Cost Implications
Insurance companies often offer lower rates for steel buildings due to their superior durability and fire resistance. Steel structures are less likely to suffer catastrophic damage from natural disasters, and their fire-resistant properties can result in significant insurance premium savings.
Additionally, steel buildings typically have longer warranties than traditional construction, which can provide added peace of mind and potential cost savings over time. Many insurance companies recognize these advantages by offering preferential rates for steel construction.
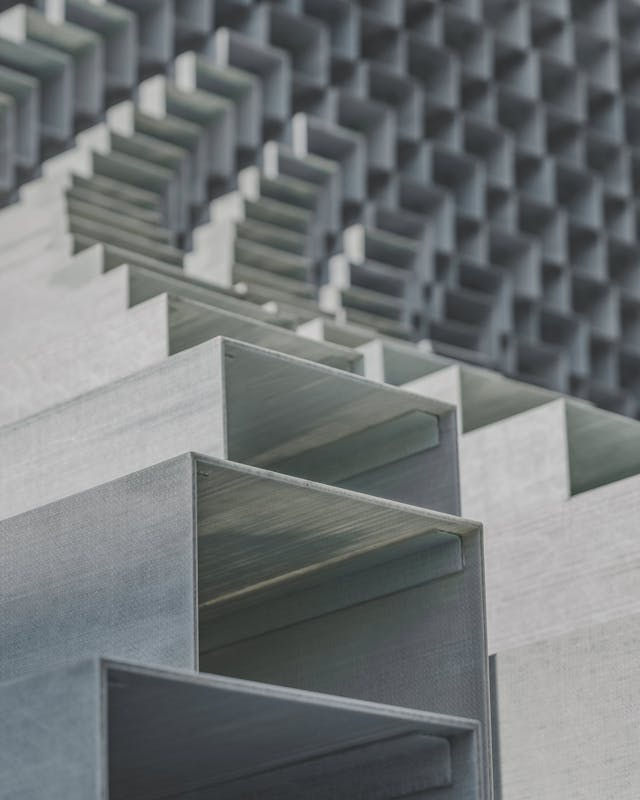
Impact on Resale Value
The resale value of steel buildings has traditionally been a concern for some homeowners. However, as awareness of their benefits grows and more people seek sustainable, low-maintenance housing options, steel buildings are increasingly seen as valuable investments.
The durability, energy efficiency, and lower maintenance requirements of residential steel building kits can be strong selling points. Modern steel buildings can also be designed to look virtually indistinguishable from traditional construction, addressing aesthetic concerns that might have impacted resale value in the past.
Environmental Considerations
Steel construction offers several environmental advantages over traditional building methods. Steel is 100% recyclable, and most modern steel products contain a significant percentage of recycled material. The precision manufacturing of steel building components also results in minimal waste during construction.
Wood construction, while renewable, can contribute to deforestation and requires significant energy for processing and treatment. The longer lifespan of steel buildings also means less frequent replacement and reconstruction, reducing the overall environmental impact over time.
Customization and Design Flexibility
Modern residential steel building kits offer extensive customization options. Advances in manufacturing and design software allow for virtually unlimited architectural possibilities, from traditional home styles to contemporary designs. Steel's strength enables large open spaces and high ceilings that would be difficult or impossible to achieve with wood framing.
Interior finishing options are equally flexible, with steel buildings able to accommodate any standard interior materials and designs. The precision of steel construction can also make it easier to install custom features and modifications both during initial construction and in future renovations.
Building Code and Permit Considerations
Building codes and permit requirements vary by location, but steel buildings generally meet or exceed most local building codes. The engineered nature of steel construction means that structural calculations and load ratings are precisely known, which can simplify the approval process.
However, some jurisdictions may have specific requirements for steel construction, particularly in residential areas. It's essential to research local building codes and obtain necessary permits before beginning construction. Many manufacturers of residential steel building kits can assist with this process and provide required engineering documentation.
Final Thoughts
The choice between residential steel building kits and traditional construction methods depends on various factors, including budget, timeline, location, and personal preferences. While steel construction typically requires a higher initial investment, the long-term benefits of durability, lower maintenance, energy efficiency, and environmental sustainability can make it a more cost-effective choice over time.
As construction technology continues to advance and environmental concerns become increasingly important, steel building kits represent a forward-thinking approach to residential construction. Their combination of strength, efficiency, and versatility makes them a compelling alternative to traditional building methods for many homeowners.
Understanding these differences and advantages can help you make an informed decision about which construction method best suits your needs. Whether you choose steel or traditional construction, careful planning and consideration of these factors will contribute to the success of your building project.
Comments